Imagine trying to bring the irregularly shaped, cartoonesque objects from the pages of Dr. Seuss' books to life. How would you do it? Curved, organic shapes and structures are difficult to create using traditional manufacturing methods-requiring the craftwork of designers, builders, or architects. But two BU computer scientists think that custom manufacturing should be more accessible to the average layperson. Now, they've combined computer science with a fabrication process known as fabric formwork, making it a whole lot easier to create large-scale custom shapes from scratch.
Emily Whiting, a BU College of Arts & Sciences assistant professor of computer science, and Xiaoting Zhang, a postdoctoral research fellow in Whiting's lab, and collaborators from the University of Hong Kong have developed a software algorithm that calculates how to cheaply and easily craft architectural objects using just fabric, plaster, a sewing machine, and a little bit of patience. Their method makes use of the centuries-old technique of fabric formwork, which involves pouring casting fluid, like plaster or concrete, into a fabric casting mold that is suspended and supported by a wooden frame.
"You're using this idea of equilibrium, how fabric hangs under the pressure of casting fluid," explains Whiting, director of BU's Shape Lab.
Taking direction from their algorithm, Whiting and Zhang have used fabric formwork to create complex objects ranging from shapely chairs to a sculpture that looks like a giant rubber duck.
Yes, the research team made a plaster "rubber ducky," and its existence could help revolutionize fabrication. They also published a paper about their work, Computational Design of Fabric Formwork, and presented their findings at SIGGRAPH, an internationally known graphic design conference, on August 1, 2019.
In this video, learn how to create objects with the team's fabric formwork technique. Video by Xiaoting Zhang
"There is a lot of use for this in architecture, because [using fabric formworks] we are not limited to simple shapes," says Zhang.
Casting objects in fabric requires less technological resources compared to 3D printing, and it is a quicker process. (3D printers can often take days to complete large objects.) Fabric formworks can even fabricate irregularly shaped objects that would be much too large for a standard 3D printer to handle, according to Whiting. Fabric also overcomes the design limitations associated with using traditional molds made of stiff plywood and other framing materials. Since the materials involved in making fabric molds are low-cost and widely accessible, the researchers hope to eventually apply their technique to large-scale architectural projects.
So, how exactly did Whiting and Zhang create an oversized plaster duck by starting with a software algorithm? First, they imported the shape of the duck into their software. (Any computer model, online shape databases, or 3D scans of physical objects can be used as an input.) The computer model is then translated, thanks to the algorithm's careful calculations, into flat sections. Those sections determine the shape of the fabric panels that are sewn together to create a fabric mold. The software provides detailed instructions on how to assemble the fabric outlines and seam locations, where to attach external support strings, and then how to suspend the formwork from the strings within a rigid outer frame.
"We envision it to be similar to sewing patterns for garments," says Whiting.

Every detail counts; the stretch of the fabric, the direction of the stitch, the seam, how the fabric is hung, how the fabric is secured to the frame. Whiting and Zhang learned to keep sagging corners upright by attaching a tiny piece of string from the corner of the mold to the facing edge of the rigid frame.
Once the fabric mold is situated, liquid casting material, like plaster, is poured into the openings of the formwork. The material cures, solidifies, and-voilà!-the fabric can be removed and you have yourself a one-of-a-kind object.
The voilà moment, however, didn't come easy at first. It took more than two years of optimizing the software's algorithm before the research team successfully created their first prototype, a shape known as the fertility model, made up of delicate curves representing a mother holding a child.
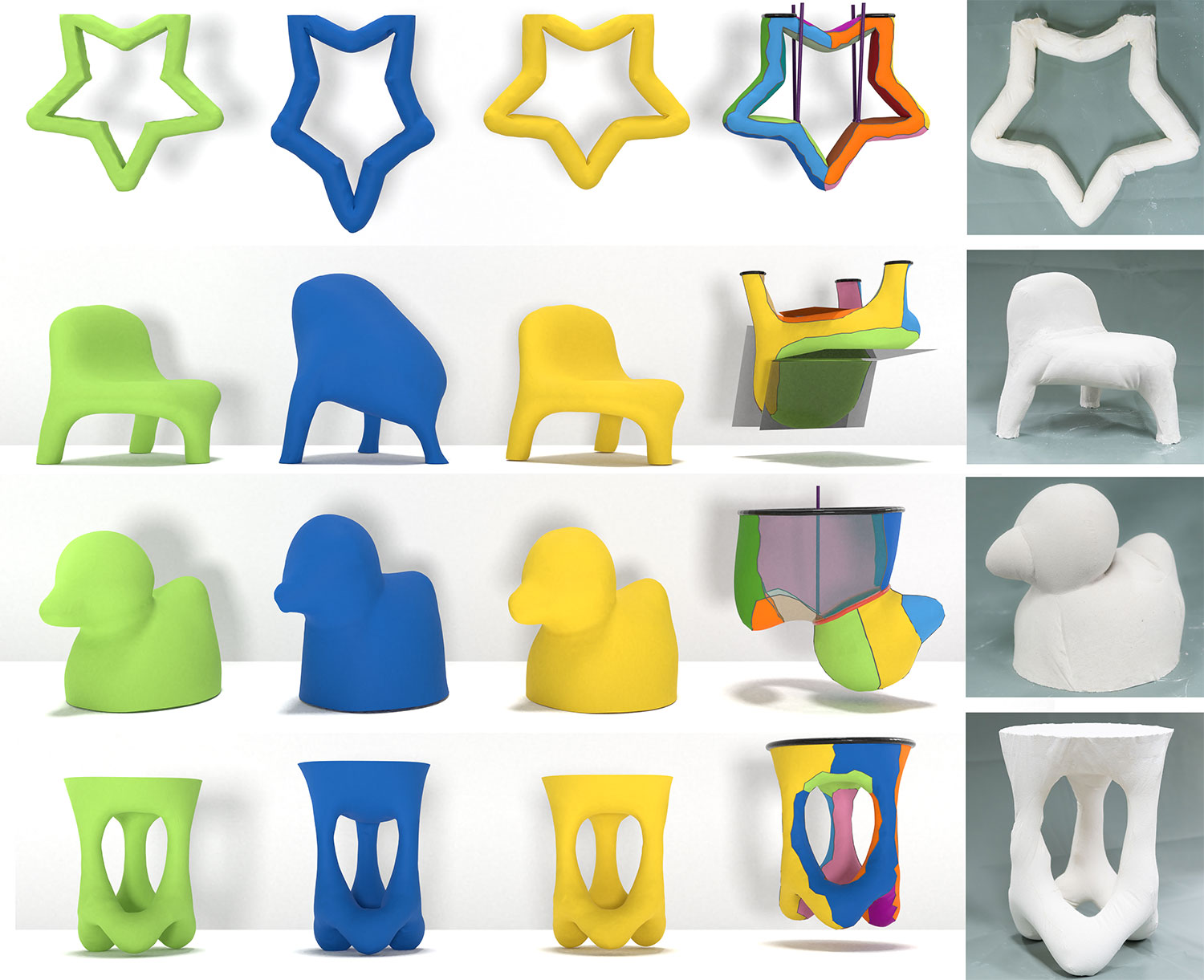
Although there are still minor kinks to work out (literally-Zhang is determined to have as few wrinkles as possible visible on the finished products), the researchers envision their technique could revolutionize fabrication in remote locations, since the fabric and frames are light enough to be easily transported and the software could be brought virtually anywhere on a laptop. They also envision the technique could be adopted by DIY crafters and designers to make custom objects right at home.
"This can make large construction processes more accessible to people with limited resources," says Whiting.