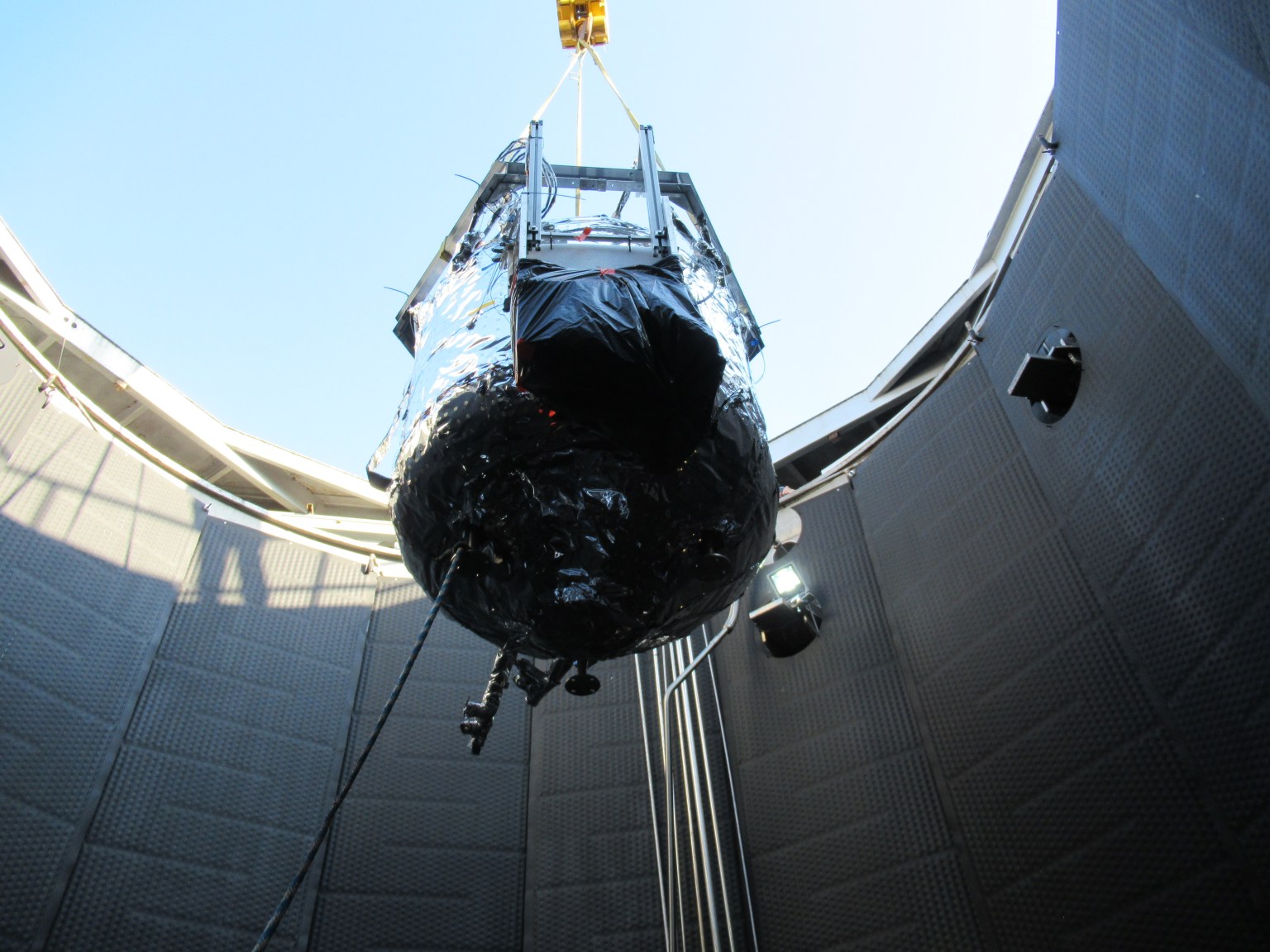
In the vacuum of space, where temperatures can plunge to minus 455 degrees Fahrenheit, it might seem like keeping things cold would be easy. But the reality is more complex for preserving ultra-cold fluid propellants - or fuel - that can easily overheat from onboard systems, solar radiation, and spacecraft exhaust. The solution is a method called cryogenic fluid management, a suite of technologies that stores, transfers, and measures super cold fluids for the surface of the Moon, Mars, and future long-duration spaceflight missions.
Super cold, or cryogenic, fluids like liquid hydrogen and liquid oxygen are the most common propellants for space exploration. Despite its chilling environment, space has a "hot" effect on these propellants because of their low boiling points - about minus 424 degrees Fahrenheit for liquid hydrogen and about minus 298 for liquid oxygen - putting them at risk of boiloff.
In a first-of-its-kind demonstration, teams at NASA's Marshall Space Flight Center in Huntsville, Alabama, are testing an innovative approach to achieve zero boiloff storage of liquid hydrogen using two stages of active cooling which could prevent the loss of valuable propellant.
"Technologies for reducing propellant loss must be implemented for successful long-duration missions to deep space like the Moon and Mars," said Kathy Henkel, acting manager of NASA's Cryogenic Fluid Management Portfolio Project, based at NASA Marshall. "Two-stage cooling prevents propellant loss and successfully allows for long-term storage of propellants whether in transit or on the surface of a planetary body."
The new technique, known as "tube on tank" cooling, integrates two cryocoolers, or cooling devices, to keep propellant cold and thwart multiple heat sources. Helium, chilled to about minus 424 degrees Fahrenheit, circulates through tubes attached to the outer wall of the propellant tank.

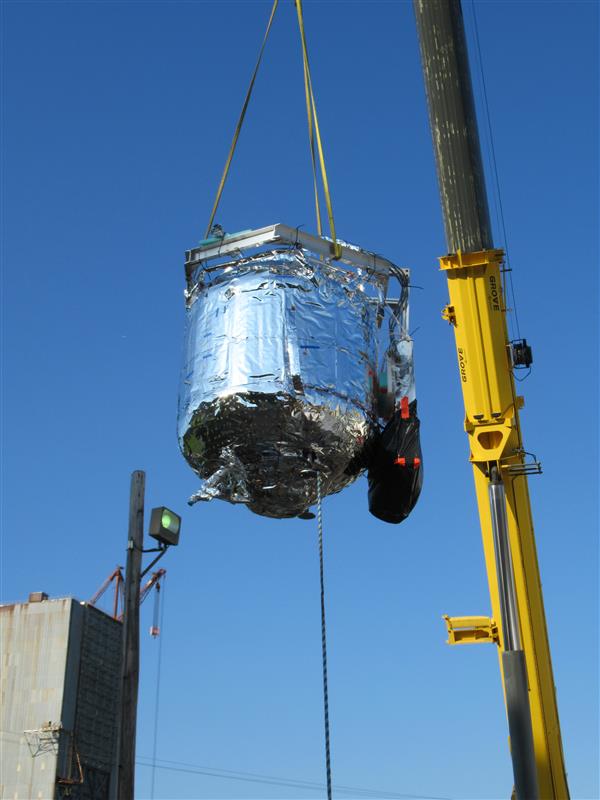
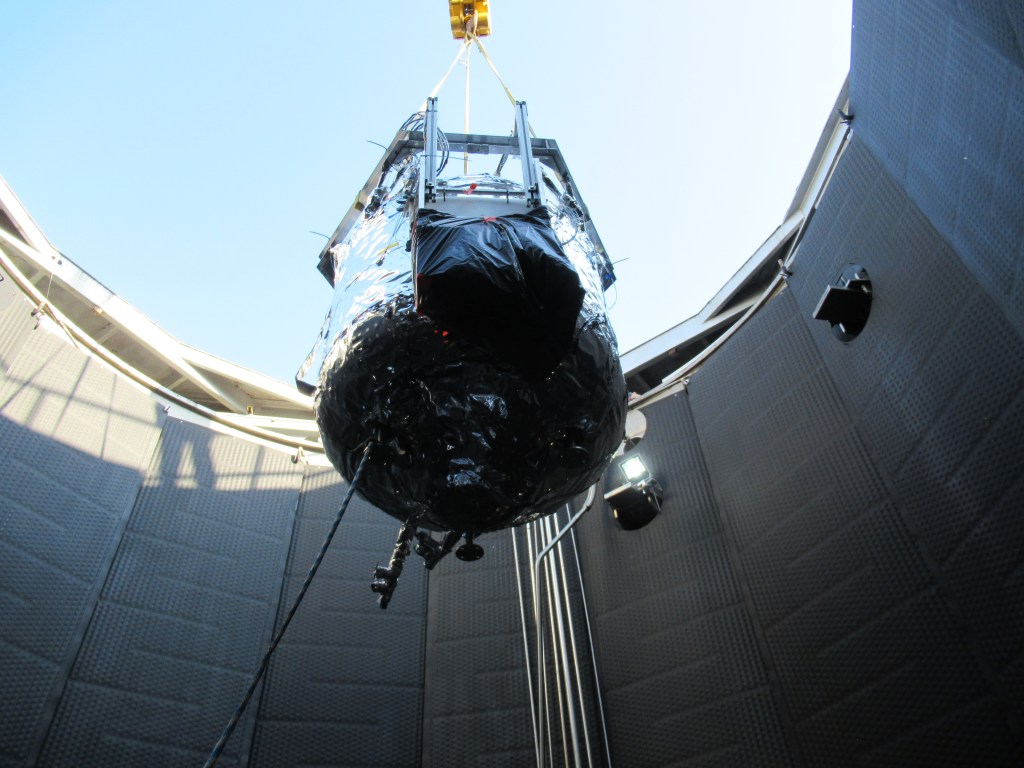
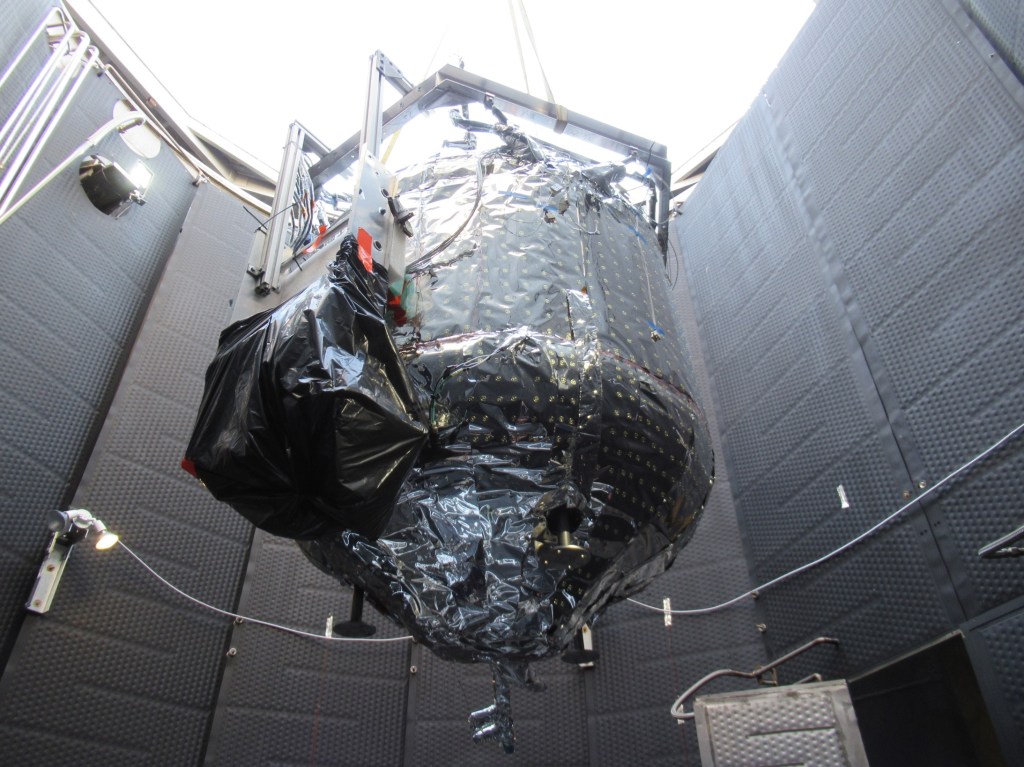
Teams installed the propellant tank in a test stand at NASA Marshall in early June, and the 90-day test campaign is scheduled to conclude in September. The tank is wrapped in a multi-layer insulation blanket that includes a thin aluminum heat shield fitted between layers. A second set of tubes, carrying helium at about minus 298 Fahrenheit, is integrated into the shield. This intermediate cooling layer intercepts and rejects incoming heat before it reaches the tank, easing the heat load on the tube-on-tank system.
To prevent dangerous pressure buildup in the propellant tank in current spaceflight systems, boiloff vapors must be vented, resulting in the loss of valuable fuel. Eliminating such propellant losses is crucial to the success of NASA's most ambitious missions, including future crewed journeys to Mars, which will require storing large amounts of cryogenic propellant in space for months or even years. So far, cryogenic fuels have only been used for missions lasting less than a week.
"To go to Mars and have a sustainable presence, you need to preserve cryogens for use as rocket or lander return propellant," Henkel said. "Rockets currently control their propellant through margin, where larger tanks are designed to hold more propellant than what is needed for a mission. Propellant loss isn't an issue with short trips because the loss is factored into this margin. But, human exploration missions to Mars or longer stays at the Moon will require a different approach because of the very large tanks that would be needed."
The Cryogenic Fluid Management Portfolio Project is a cross-agency team based at NASA Marshall and the agency's Glenn Research Center in Cleveland. The cryogenic portfolio's work is under NASA's Technology Demonstration Missions Program, part of NASA's Space Technology Mission Directorate, and is comprised of more than 20 individual technology development activities.