In spring 2020, as news spread of N95 mask and ventilator shortages in hospitals, researchers at U.S. Department of Energy (DOE) national laboratories sprang into action. As part of the Coronavirus Aid, Relief, and Economic Security (CARES) Act, the DOE Office of Science's National Virtual Biotechnology Laboratory provided support to a consortium of 16 national laboratories tasked with doing the research to help address these critical shortages.
A team of seven Pacific Northwest National Laboratory (PNNL) engineers took on the challenge of how to assure that ventilators would not sit idle because crucial consumable components were in short supply. Prior to the COVID-19 pandemic, ventilator breathing circuit components were typically imported. But the increased demand for ventilators and their parts, along with stress on the global supply chain, prompted the call for a U.S.-based manufacturing solution.
To ensure a ready supply of ventilator parts for hospitals, the PNNL engineers set to work in April, taking apart ventilator breathing circuit and figuring out how to create molds that would allow manufacturers to use new manufacturing approaches to produce parts on demand.
Michelle Fenn, a mechanical engineer at PNNL, was part of that team, which used 3D printing, also known as additive manufacturing, to custom-design single-use ventilator ports-the pieces that can't be cleaned and reused between patients. They created designs for air supply junctions and the ports that doctors use to administer the medications that help patients breathe easier. The designs included two sizes of ventilator parts, one for adults and one for children.
Custom fit for all face shapes
With so many people relying on homemade cotton face shields to protect themselves and others, PNNL engineers puzzled out a way to customize the fit to reduce air gaps that decrease effectiveness. They designed a unique customized face covering frame design that can be used by anyone. It may be of particular interest to people at higher risk of serious, life-threatening complications from contracting COVID-19. The frame design uses the same kind of materials used in athletic mouth guards. When the material is soaked in warm water, it becomes pliable and can then be fitted to the face for a custom fit.
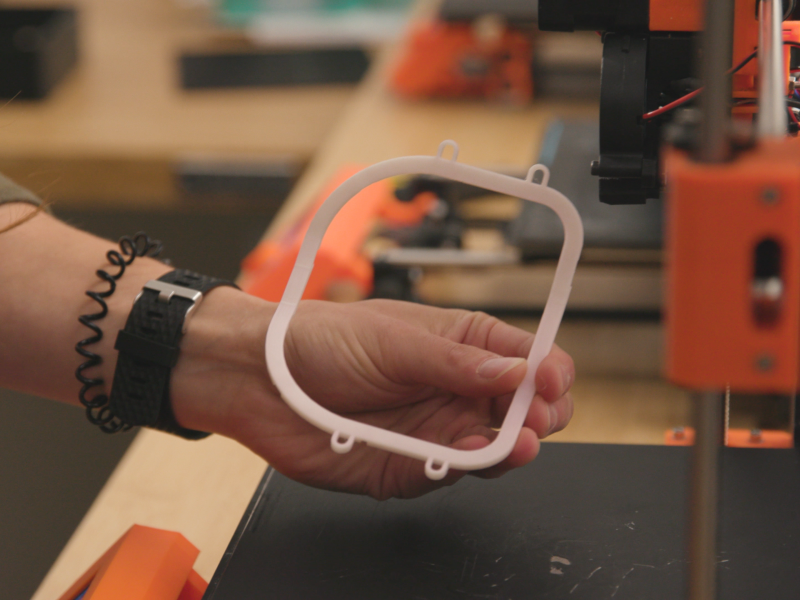
Addressing the shortage of N95 material
The design team also created a prototype for a respirator mask that uses less N95 filter material than a standard disposable mask, which would enable more masks to be made from the same volume of N95 material. To surface the best possible final design, each national laboratory in the consortium worked independently on mask designs. Once prototypes had been developed, the engineers worked together to optimize these masks for rapid manufacturing.
"Many of our masks designs can be vacuum-formed, which is an incredibly rapid manufacturing technique," said Fenn. "We have explored multiple materials to find ones that are comfortable to wear and are easily adjusted to each user."
Rapid response requires fast prototyping
PNNL's additive manufacturing facility works primarily with the same kind of 3D printers used by hobbyists. The engineers focus on understanding the limits of these printers and the different kind of materials that can be deployed successfully using these devices. For example, a PNNL team recently used 3D printing technology to make a prototype framework for energy applications.
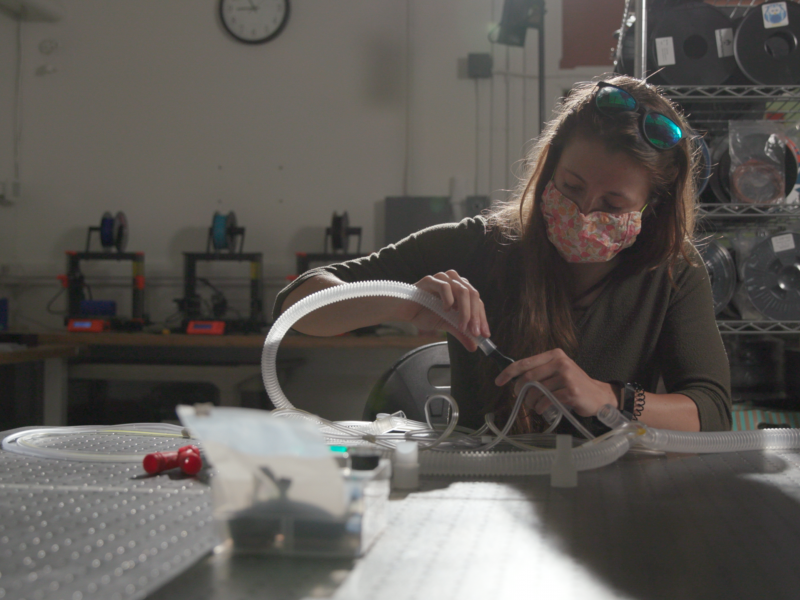
For the COVID-19 research, time was of the essence, and the PNNL team had only three months to obtain ventilator circuit components, produce workable prototypes, and test them for fit and durability. After completing the design and prototype phase in June, the team turned over its designs to partners at other national laboratories for additional rigorous characterization and testing and, potentially, for transition to manufacturers. The capabilities across the national laboratories could enable surge capabilities in producing small parts at low volume or developing molds for larger manufacturing demands.
"Additive manufacturing lends itself very well to being able to solve this challenge by being able to prototype very quickly and iterate on designs," said Fenn.
With the design phase of the project now complete, the masks and ventilator specifications have been made freely available as part of an initiative to accelerate technology development during the COVID-19 pandemic.
"Now that we have finalized our designs, we have sent them on to other national labs that focus more on prototyping leading to mass production," Fenn said. The ventilator designs have been transferred to Idaho National Laboratory, which will move into the manufacturing phase. The designs would allow a company to make a U.S. Food and Drug Administration-compliant injection mold for producing these parts in large scale for distribution to hospitals. Ames Laboratory will develop and test the face frame design and may make it available for a manufacturing partner.
"It's really fulfilling to have your design go out into the world and make an impact," Fenn added.
Oak Ridge National Laboratory is leading the overall effort to address the need to manufacture medical supplies in short supply and high demand during the COVID-19 pandemic. Learn more about how the National Virtual Biotechnology Laboratory is working to address shortages of personal protective equipment.