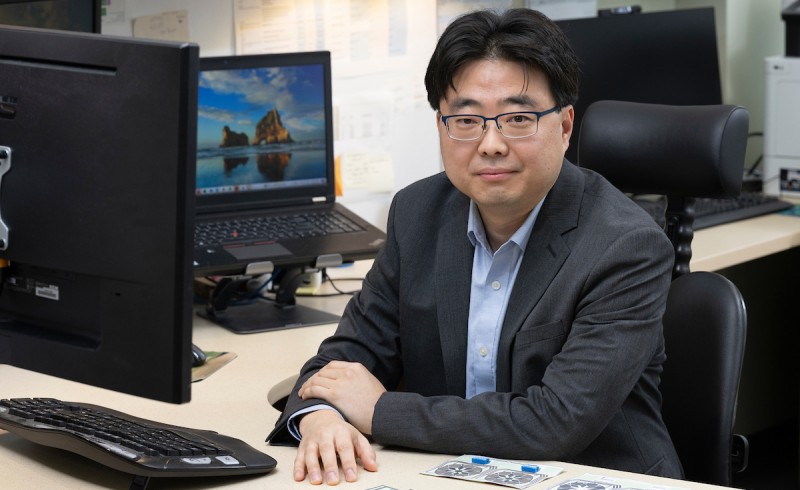
Engineering innovations generally require long hours in the lab, with a lot of trial and error through experimentation before zeroing in on the best solution.
But sometimes, if you're lucky, the answer can be right under your nose - or in this case, beneath your feet.
Binghamton University Professor Seokheun "Sean" Choi has developed a series of bacteria-fueled biobatteries over the past decade, building on what he learns to improve the next iteration. The biggest limitation isn't his imagination - he's always juggling several projects at once - but the materials he has to work with.
When Choi - a faculty member in the Thomas J. Watson College of Engineering and Applied Science's Department of Electrical and Computer Engineering - needed a collaborator who could create a specialized stainless-steel component, he found someone just downstairs from his office at Binghamton's Engineering and Science Building.

It turns out that Assistant Professor Dehao Liu from Watson's Department of Mechanical Engineering is an expert in laser powder bed fusion (LPBF) technology, a new method for the printing of stainless-steel microarchitectures.
"LPBF is ideal for biobatteries because it enables high-precision, customizable 3D structures with complex geometries, essential for maximizing surface area and energy density," Liu said.
They recently published a paper in the journal Advanced Energy & Sustainability Research outlining their findings, which could help to power small, autonomous devices such as sensors for the Internet of Things that increasingly connects everything in our lives.
Other researchers on the project are ECE Assistant Professor Anwar Elhadad, PhD '24 (Choi's former student); Yang "Lexi" Gao (his current PhD student); as well as Liu's PhD students, Guangfa Li and Jiaqi Yang. Funding the research is Choi's 2024 grant from the National Science Foundation.

"I'm so happy about this collaboration," Choi said. "It makes this iteration of the biobattery very meaningful to me."
How it works
Endospores provide the fuel for an electrochemical reaction that generates electric current. These dormant forms of bacteria show exceptional resilience from environmental stresses and activate when conditions are favorable.
The biobattery needs three components to function: a positive electrode (the cathode), a negative electrode (the anode) and a membrane where ions exchanged between the two generate an electric current. For the best power output, the anode - where the bacteria are - needs to be three-dimensional, so that the organisms can colonize and thrive in the least amount of space.
"A two-dimensional anode is not efficient," Choi said. "Nutrients will not be delivered effectively to the bacteria, and their waste cannot go out effectively."

Complicating the production of 3D anodes is that carbon-based or polymer-based materials have low electrical conductivity and are often too fragile for everyday use. Their microfabrication processes also require high temperatures, which can be deadly to bacteria.
"Two years ago, we started to use stainless steel mesh as an anode, because its conductivity is really good and it's structurally very strong," Choi said. "We were successful integrating the microbial fuel cell into electronics like this. The problem with commercially available mesh is that we cannot control the porosity and roughness of it. We'd just buy it and then drop in bacterial cells."
The LPBF process deposits a layer of metal powder, melts and then solidifies it using a laser to create a solid layer of metal, and those two-dimensional layers join up to build 3D components. Details for the printed piece can be planned down to the nanoscopic level.
"We saw the potential here," Choi said. "Then we prepared other components using 3D printing as well, like a sealing cover and the cathode part, and we simply assembled them like Lego bricks."

The biobatteries can be stacked in series or parallel to increase output, with six batteries achieving nearly 1 milliwatt - enough to power a 3.2-inch thin-film transistor liquid crystal display. It's one of the highest electrical outputs that Choi has achieved among his biobattery designs.
Choi noted that the stainless-steel components have another advantage: "You can detach the bacterial cells and then reuse them, and we showed after a number of uses that power levels are maintained."
'Inspiring' innovation
For Elhadad, this latest paper directly follows from doctoral research he did as Choi's student.
"My PhD focused on developing bioelectronic systems that integrate sustainable energy-harvesting technologies, particularly microbial fuel cells," he said. "This research builds on that foundation by addressing some of the key challenges I encountered during my dissertation - particularly the need for scalable, high-performance and structurally robust electrode materials."
Elhadad added that working with Choi is "inspiring and intellectually stimulating."
"He encourages creativity and pushes the boundaries of what's possible, especially when it comes to integrating biology with electronics," he said. "Our collaboration is very hands-on - from designing experiments to troubleshooting materials and fabrication techniques. He has a clear vision but is always open to new ideas, which made our work feel both structured and innovative."
Looking ahead, the Binghamton team would like to devise a unified printing method for the biobattery components, rather than creating each of them separately. Another goal is to improve energy harvesting through a power management system to control the charging and discharging of the battery, similar to a solar cell.