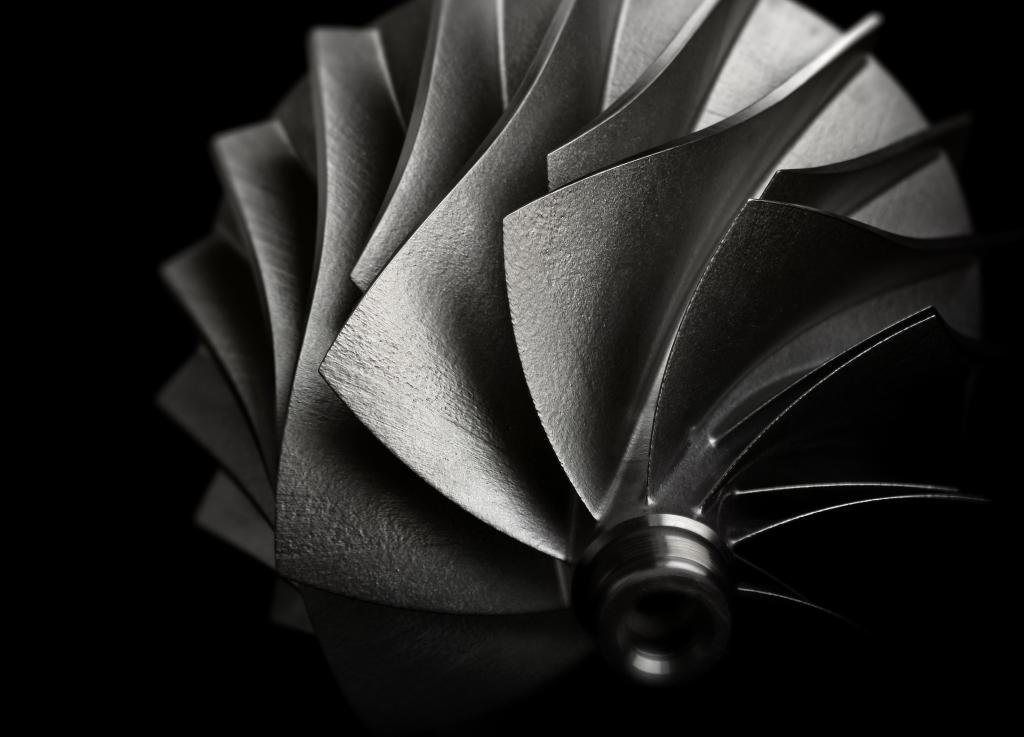
When Jonaaron Jones started his master's degree at the University of Tennessee, Knoxville, his mentor invited him to visit the Manufacturing Demonstration Facility, or MDF, at Oak Ridge National Laboratory. "I saw a metal 3D-printed part for the first time," said Jones. "I knew I was seeing the future - for industry and for me."
Over the next few years, Jones worked in the MDF alongside advanced manufacturing experts from UT and ORNL. His experiences there launched him on a cutting-edge career path in additive manufacturing for aviation, defense and energy applications, first as founder of start-up Volunteer Aerospace and now as part of Beehive Industries , a U.S.-based additive manufacturing company that specializes in the design and development of jet engines for defense applications as well as parts manufacturing. With Jones as president and general manager of its external parts business, Beehive continues to demonstrate what it means to partner with the MDF to drive technical and economic growth for the United States.
Volunteers in action
As Jones's mentor, Suresh Babu, former UT-ORNL Governor's Chair of Advanced Manufacturing, connected him to MDF experts and resources, as well as partners within the aerospace, defense and energy industries.
In 2015, Babu led UT and MDF researchers in a project with industry partner Aerojet Rocketdyne that was supported by the Air Force Research Laboratory and the Defense Production Act under the federal Title III cost-share program. Jones and other team members sought additive manufacturing solutions to aerospace supply chain challenges, including long lead times and quality issues for cast parts.
Specifically, they set out to 3D print aluminum parts for the RL10 liquid rocket engine manufactured by Aerojet Rocketdyne. Aluminum for additive manufacturing was still very low in technology readiness at that time, and they faced challenges from the start due to a lack of material and machine options.
"We essentially had to apply aluminum powder atomized for other applications, like automotive," Jones said. "We learned that powder requirements were different. For example, we had to correct for moisture content."
The team also had to find a machine big enough to produce rocket parts. At that time, the largest on the market was Concept Laser's X-Line 1000, intended for prototyping small automotive engine blocks. The team set up one of these machines in the MDF.
"The rocket parts at least fit inside, but it wasn't designed for the level of quality we needed," Jones said. "I volunteered to take on making the machine usable for our project. I realized I had all the people and resources I needed at my fingertips. I worked with different groups around the lab to identify problems, solve them at the basic science level, apply the fixes and test them. A company doing this on its own wouldn't have had that advantage. After we worked on the machine and the material feedstock, the difference was night and day."
At the end of the program, Aerojet Rocketdyne decided not to relocate this printer to its production facilities. Title III requirements, however, meant the equipment must be used to develop the defense supply chain.
Jones and two soon-to-be business partners - his wife Rachel Cade Jones and ORNL colleague Devon Burkle - envisioned a solution. In 2016, they sought approval from all entities involved in the project to start their own business, Volunteer Aerospace.
In 2017, they moved the X-Line 1000 printer out of the MDF into a facility 10 minutes away. Volunteer Aerospace soon added new employees, machines and clients including Boeing, Lockheed Martin and Northrop Grumman.
"We became the industry leader in large aluminum parts," Jones said. They also supported the MDF on material development and other ORNL teams on small yet complex projects, such as printing a distillation column for carbon capture.
Volunteer Aerospace caught the attention of Beehive Industries. Beehive acquired Volunteer Aerospace in 2021 to support its vision of powering American defense by scaling its core capabilities, employee base and resources.
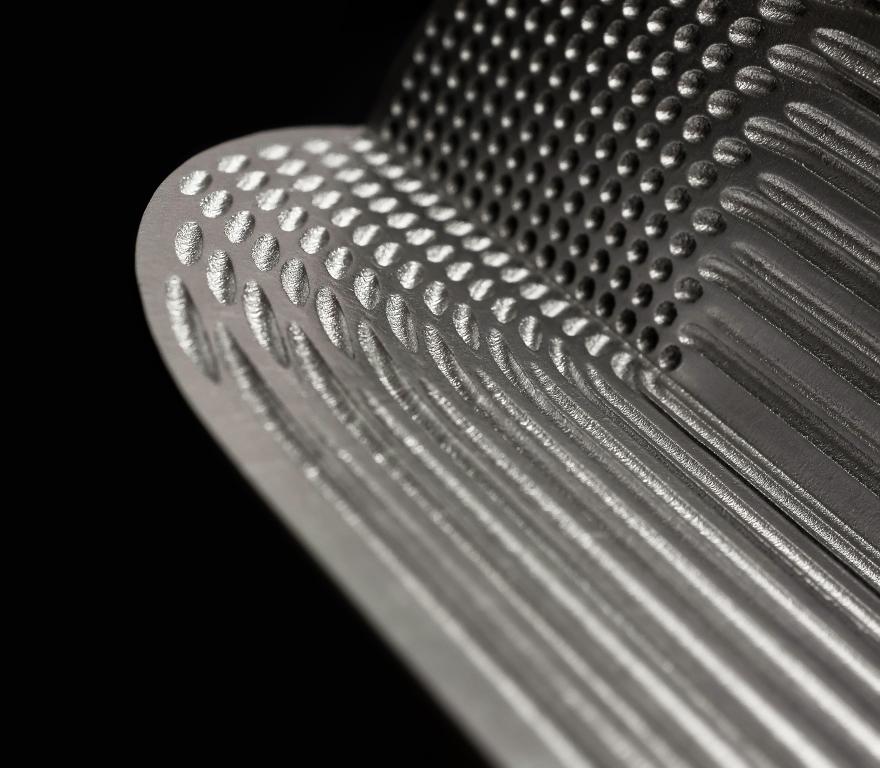
Catalyzing an ecosystem for success
"Ninety-eight percent of manufacturing happens at small and medium enterprises like Volunteer Aerospace," said Craig Blue, ORNL chief manufacturing officer. "Bringing manufacturing to a region, developing supply chains and commercializing new technologies are heavy lifts that one entity, no matter the size, can't achieve alone. It takes an ecosystem.
"The MDF's unique public-private partnership model is a catalyst for developing that ecosystem, and we are bringing small and medium companies into it so they can succeed more rapidly."
ORNL's Ryan Dehoff, director of the MDF, said this ecosystem aligns with DOE's mission.
"It's where industry, academia and government come together to tackle big challenges across the entire supply chain, and where the workforce connects with training and experience. Together, it's a whole that's greater than the sum of its parts," Dehoff said.
The nationwide network radiates out from a regional hub in East Tennessee, which lies within a day's drive of 65% of the United States' population - and roughly two-thirds of its manufacturing base. Within the ecosystem, MDF engages with more than 1,000 entities each year, including industry partners from every sector as well as more than 50 universities to drive scientific advancement, technology deployment and economic growth.
Blue said the evolution of Volunteer Aerospace "is an incredibly strong success story in the ecosystem, and it continues with Beehive Industries."
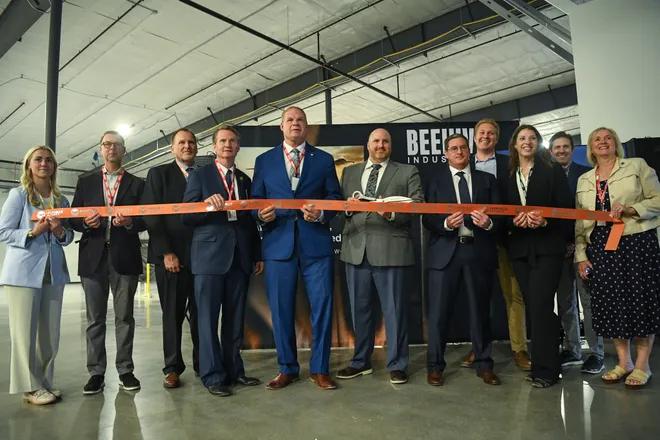
Open for growth and employment
Since acquiring Volunteer Aerospace, Beehive has scaled up its presence in East Tennessee by opening a $4 million, 60,000-square-foot facility in Knox County in May 2024.
"Proximity to the MDF was key for Volunteer Aerospace, and now for Beehive," said Jones. "It's still the first place we turn to talk through challenges. Recently, they've been a huge resource as we get more into machining additive manufactured parts."
"Being nearby also helps us collaborate with other companies in the ecosystem," Jones added. "When Boeing visits the MDF, for example, it's simple to take the short drive to our new facility."
The facility is producing and validating primary jet engine hardware components - and creating new high-technology jobs. Over time, Beehive expects local employment to exceed 150 people in roles related to manufacturing, engineering and machining.
"We're also thinking about how to train and integrate the next generation of professionals," Jones said. To do that, Beehive is tapping into programs at UT, the Tennessee College of Applied Technology and other local institutions. The Beehive team is also excited about Pellissippi State Community College's new aviation technology degree .
Looking to the future
"In Beehive's external parts business, it's our job to stay on the cutting edge to serve the company and service our customers' needs," Jones said. For example, Beehive Industries has worked alongside the MDF in a long-term initiative to develop, test and set up the supply chain for a next-generation aluminum alloy designed for aerospace applications.
"The MDF gives us a window into the future, right next door," Jones added. "We get to see what technologies are coming down the pike in five years and think now about how to integrate those into our products and processes."
Beehive's market segment - laser powder bed printing for defense, aviation and energy - has seen significant growth year over year. "We don't see that stopping," Jones said. "Additive manufacturing has become a standardized production offer, and work coming out of the MDF and ORNL has significantly influenced that. The more demand keeps growing, the more jobs we can continue creating."
"Jonaaron and Beehive are advancing the science while building the ecosystem," Babu said. "We want to see even more companies and universities get involved in both, so that together, we can create more success stories and economic growth."
The MDF, supported by Department of Energy's Advanced Materials and Manufacturing Technologies Office, is a nationwide consortium of collaborators working with ORNL to innovate, inspire and catalyze the transformation of U.S. manufacturing. Learn more about working with the MDF .
UT-Battelle manages ORNL for DOE's Office of Science, the single largest supporter of basic research in the physical sciences in the United States. DOE's Office of Science is working to address some of the most pressing challenges of our time. For more information, visit energy.gov/science . - Meghan McDonald