A composite material with metal layers of varying hardness can be produced through clever temperature variation
The material has a legendary reputation. Damascus steel is hard yet tough because it consists of layers of different iron alloys. In ancient times, this was the material of choice, especially for sword blades. A team from the Max-Planck-Institut für Eisenforschung in Düsseldorf and the Fraunhofer Institute for Laser Technology in Aachen has developed a process that allows this type of steel to be produced layer by layer in a 3D printer. The hardness of each individual layer can be specifically adjusted. Such composites could be of interest for aerospace components or tools produced with 3D printers.
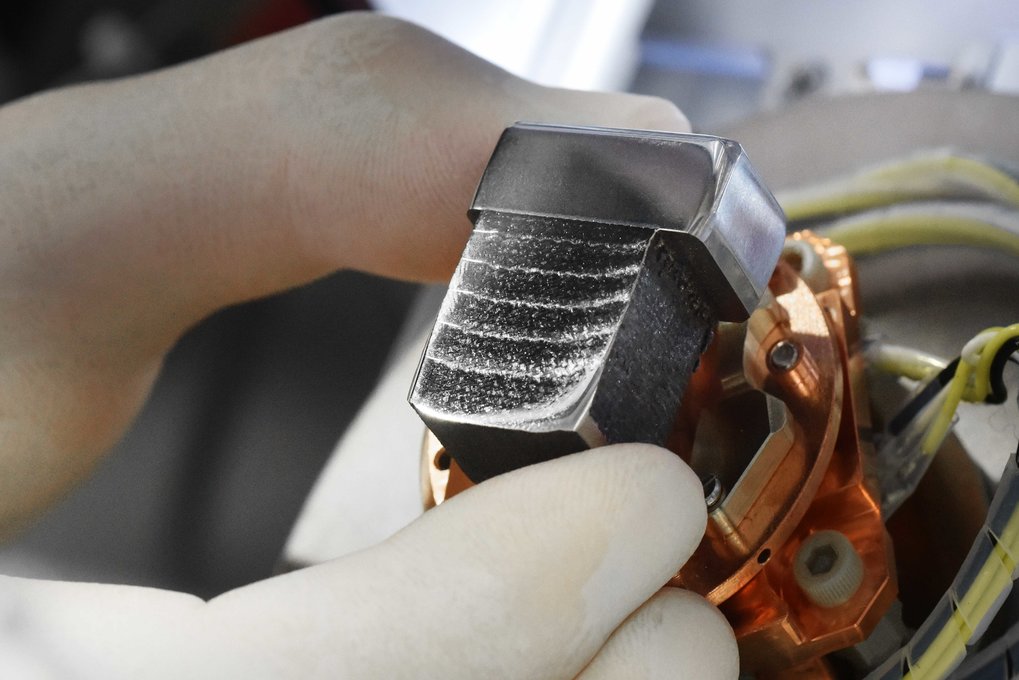
Born out of necessity and destined to become a legend. In the past, blacksmiths were able to influence the properties of iron alloys only by adjusting their carbon content. They obtained either a soft yet tough or a hard yet brittle steel. Especially for swords, a tough and hard material was needed so that the blades would not break or have to be straightened in the middle of a battle.
Celtic smiths combined various iron alloys (perhaps initially only to recycle the valuable iron) and thus obtained the material that later became known as Damascus steel or damask. It owes its name to the trading centre through which the composite material of oriental origin entered Europe. While Indian and Arabic damask was created by a sophisticated smelting process, European smiths developed the art of folding two alloys into many thin layers. The layered structure of Damascus steel can usually be recognized by a characteristic stripe pattern.
The crystal structure can be changed by a laser beam
Although there are currently ferrous alloys that are both hard and tough, they are often not specifically made for the 3D printing process thus do not fully exploit the advantages of this manufacturing technique.. Scientists at the Max-Planck-Institut für Eisenforschung (MPIE) and the Fraunhofer Institute for Laser Technology have now developed a steel that consists of only a single starting material but is made up of alternating hard and ductile layers - a kind of Damascus steel, through 3D printing. "We have succeeded in specifically modifying the micro-structure of the individual layers during 3D printing so that the final component has the desired properties - and all this without subsequent heat treatment of the steel", says Philipp Kürnsteiner, post-doctoral researcher at the MPIE.
3D printers for additive manufacturing (the technical term for this process) have become standard in many industrial sectors within only a few years. They are able to produce plastic as well as metallic components. The respective alloy is added as a fine powder, melted by a laser beam, and repeatedly applied layer by layer to form the target component. For the last few years, fuel injection nozzles for aircraft engines, among other things, have been produced using this additive manufacturing method also known as laser cladding.
The laser beam allows to not only melt the respective material but also to heat the top layer of the already resolidified metal. This is exactly what the team of the Max Planck researchers in Düsseldorf used to specifically change the crystal structure of the steel in individual metal layers - and thus influence the mechanical properties without changing the chemical composition.
Pauses in the printing process allow the formation of hardening precipitates
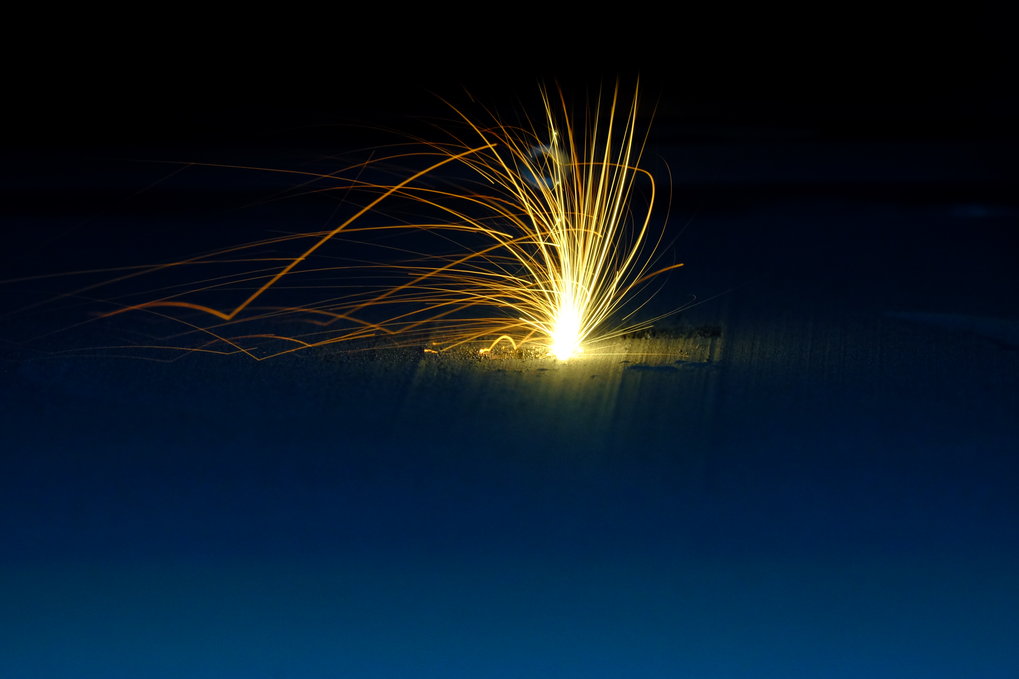
They developed an alloy consisting of iron, nickel, and titanium. At first, this alloy is relatively soft. "Under certain conditions, small nickel-titanium micro-structures form. These, so-called precipitates, harden the material", explains Kürnsteiner. "When subjected to mechanical stress, they hinder the movement of dislocations within the crystal lattice that is characteristic of plastic deformation".
In order to be able to create the nickel-titanium structures, the researchers interrupt the printing process for a certain time after each newly deposited layer. The metal cools down to below 195°C. "Below this temperature, a transformation of the crystal structure occurs in the steel", explains Eric Jägle, head of the "Alloys for Additive Manufacturing" group at the Max-Planck-Institut für Eisenforschung and, since January 2020, professor at the University of the Bundeswehr Munich. "The so-called martensite phase is formed, and only in this phase can the nickel-titanium microstructures be created." However, in order to allow precipitates to form, reheating is necessary. To achieve this reheating the researchers exploit the laser energy used to deposit the subsequent layer.
This additional effect caused by the laser beam of the 3D printer is referred to as intrinsic heat treatment. Layers that have been directly covered with the next layer without interruption remain softer because they are not yet present as martensite at this point.
For the first time, the researchers are able to create a composite material consisting of layers with different properties from a single starting material directly during the production process. Kürnsteiner is impressed by the mechanical properties of the material produced in this way: "The tests confirm an excellent combination of strength and ductility".
Objects with a soft core and hard surface
Numerous process parameters are suitable for influencing the micro-structures during 3D printing. Jägle explains that in addition to or instead of the pause time, which is varied in this study, martensite formation and subsequent precipitation hardening could also be controlled by varying the laser energy, laser focus, or printing speed as well as external heating and cooling techniques.
In their experiments, the researchers produced cube-shaped or cuboid steel pieces with side lengths of a few centimetres as models for objects with more complex geometries for which computer-controlled 3D printing is of interest. They also emphasise that the Damascus-like steel with its periodically changing layers is only one example of locally influencing the micro-structure of an alloy during the manufacturing process. For example, it is equally possible to create tool components with a continuous soft core surrounded by a hard, abrasion-resistant outer layer. "Thanks to our concept of local control, this was achieved in a single manufacturing step - without the additional process steps previously required for surface hardening such as nitriding", stresses Jägle. According to the researchers, it might also be possible to use the technology to locally adjust other properties such as corrosion resistance.
"The technology opens new doors for adjusting the local micro-structures in a defined manner during the additive production of even complex work pieces and making post-treatment unnecessary", says Kürnsteiner. The researcher also suggests a paradigm shift: "Until now, it has been common practice to use conventional alloys in 3D printing. However, many known steels are not optimally suited for additive manufacturing. Our approach is to develop new alloys that can exploit the full potential of 3D printing".
KH