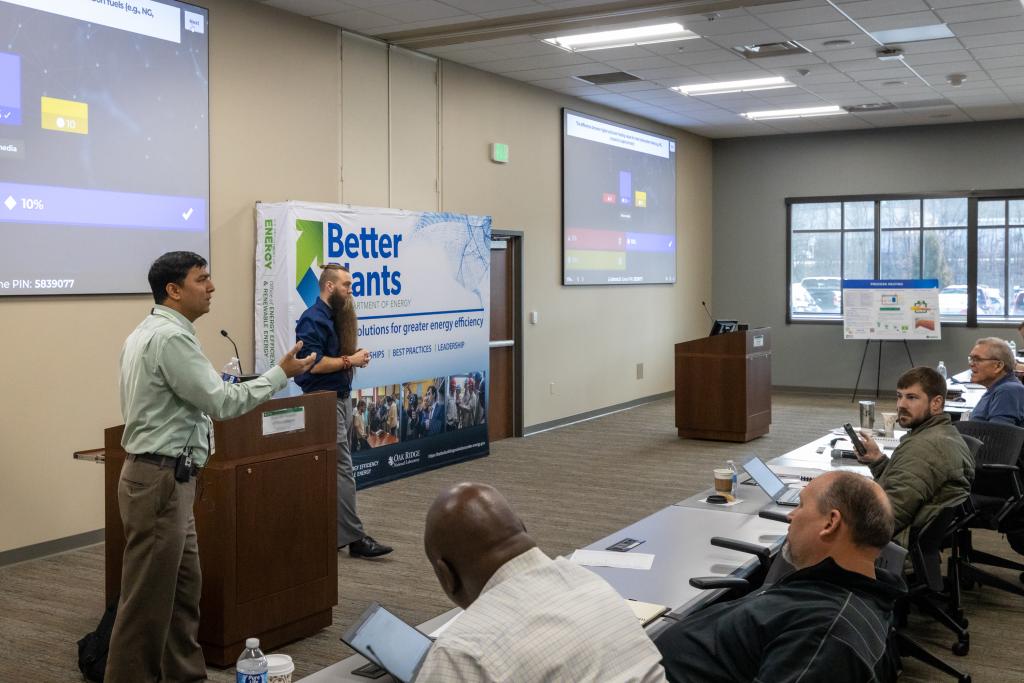
Helping hundreds of manufacturing industries across the United States increase energy efficiency requires a balance of teaching and training, blended with scientific guidance and technical expertise. It's a formula for success that researchers at Oak Ridge National Laboratory have been providing to the Department of Energy's Better Plants program for more than a decade.
ORNL's support for the program has led to Better Plants partners achieving a cumulative $11.8 billion in cost savings, 2.4 quadrillion British thermal units of energy savings and 147 million metric tons of carbon dioxide avoided, as highlighted in the most recent progress report released by DOE's Better Buildings Initiative. The Better Plants program has also helped to improve the average annual energy intensity rate by 1.8%. Energy intensity is a measure of overall inefficiency, calculating the amount of energy an industry uses to produce a product or service.
"Reducing energy intensity is one of the goals of Better Plants and the challenge we're presented with is reducing that by 25% over the next 10 years," said Sachin Nimbalkar, who leads ORNL's Manufacturing Energy Efficiency Research and Analysis group, or MEERA, which supports the program. "Manufacturing industries, particularly the industrial sector, account for one-third of the nation's energy consumption. If we can impact the energy intensity rate, we're at the same time uncovering potential energy and cost savings that can be reinvested back into the workforce and the economy."
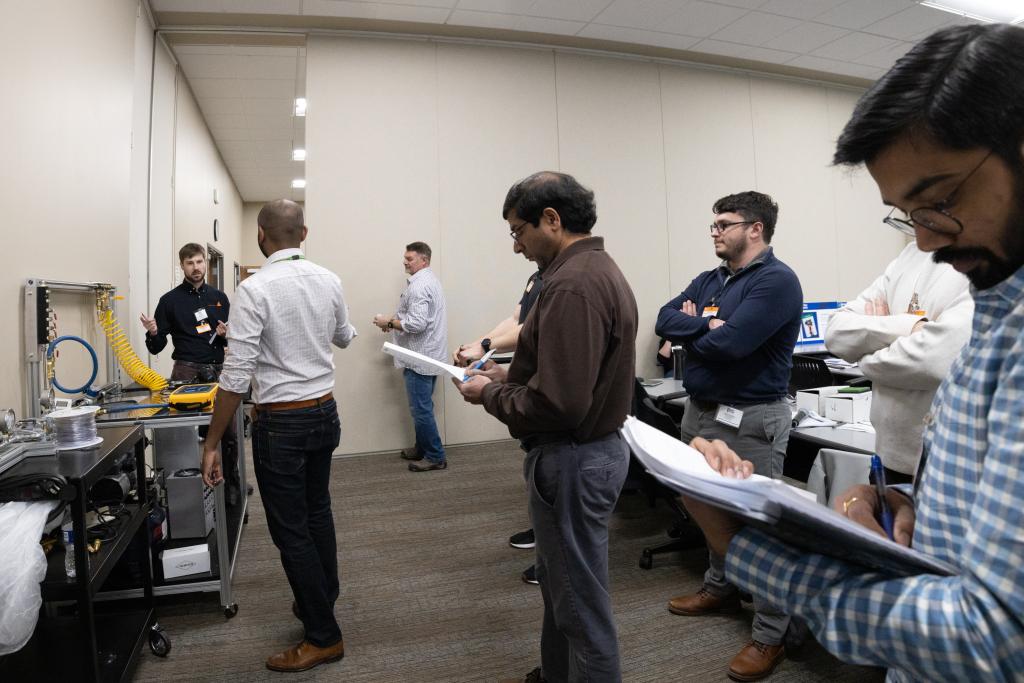
To reach that number, energy efficiency and decarbonization experts in the MEERA group work to encourage industries and water utilities to become a partner in the voluntary program. Currently, more than 280 partners have joined the Better Plants program representing automobile and transportation industries, food and beverage, consumer products, chemicals and metals, as well as water and electric utilities. Since the program's inception in 2011, partners have reported energy data across 3,600 industrial plants.
Personalized energy planning
Becoming a Better Plants program partner provides industries with access to a technical account manager from ORNL who works one-on-one to develop an energy management plan, identify savings opportunities and track performance metrics. Partners also receive support through onsite visits and trainings, including Energy Bootcamps hosted at DOE's Manufacturing Demonstration Facility, or MDF. Located at ORNL, MDF is a nationwide consortium of collaborators working to innovate, inspire and catalyze the transformation of U.S. manufacturing. The Better Plants program is supported by DOE's Industrial Efficiency and Decarbonization Office, or IEDO.
Launched in 2022, Energy Bootcamps are intense four-day training sessions where sustainability managers, energy engineers, plant operators and maintenance professionals participate in hands-on demonstrations with the ORNL team to understand how best to execute energy saving measures in their respective facilities. Since their creation, the team has conducted approximately 120 Bootcamps.
"Onsite in-plant trainings, where we're on the ground working at the industry's location for several days, have long been a standard part of our curriculum," Nimbalkar said. "The Energy Bootcamps provide an additional opportunity for partners to network and learn from each other, too."
ORNL's Decarbonization Bootcamp provides leading industrial companies and organizations the technical assistance, tools, insights and networking opportunities to drive meaningful energy efficiency and decarbonization improvements.
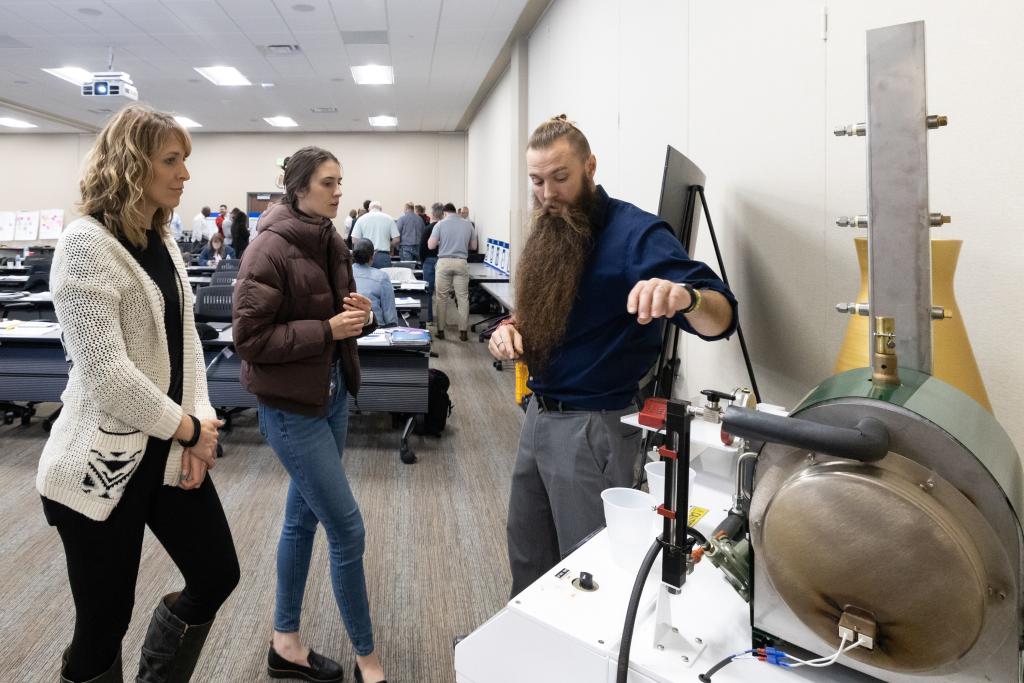
Energy Bootcamp trainings were essential to building a network of partners after the COVID-19 pandemic when onsite trainings moved to virtual platforms, which continue to be offered with an expanded webinar catalogue. Virtual and in-person trainings focus on process heating and steam systems, pumping systems, waste reduction and compressed air, wastewater treatment, ammonia refrigeration and industrial fans. Participants can learn how to use diagnostic tools - such as infrared cameras, leak detectors and combustion analyzers - to quickly identify and address issues that lead to energy loss.
Software tools, such as the ORNL-developed MEASUR that features simple calculators to assess performance and add up savings, and the Energy Footprint Tool that monitors up to 20 types of energy consumption, are open-access and easy to download and install so anyone assigned to manage energy usage in the facility can navigate. In 2023, ORNL helped the Better Plants program add another training opportunity to the roster, the first Decarbonization Bootcamp, that was designed for partners focused on using tools to reduce energy-related carbon dioxide, or CO2, emissions. The ORNL-developed VERIFI, which tracks the energy and carbon footprints, helps corporate energy managers, plant energy managers, and energy engineers benchmark, baseline, and visualize their energy usage and utility bills.
ORNL's Thomas Wenning, who manages industrial energy efficiency for the Better Plants program, said industry represents 30% of U.S. primary energy-related CO2 emissions. Carbon dioxide is among the greenhouse gas emissions, or GHGs, that are harmful to the environment and contribute to climate change.
The Decarbonization Bootcamp supports DOE's Industrial Decarbonization Roadmap that identifies pathways to reduce industrial emissions through innovation in American manufacturing by focusing on five of the highest CO2-emitting industries: petroleum refining, chemicals, iron and steel, cement and food and beverage. In addition to improving the energy efficiency of these industries, other pathways include implementing electrification processes, deploying low-carbon fuels and other energy sources and developing carbon capture, utilization and storage capabilities.
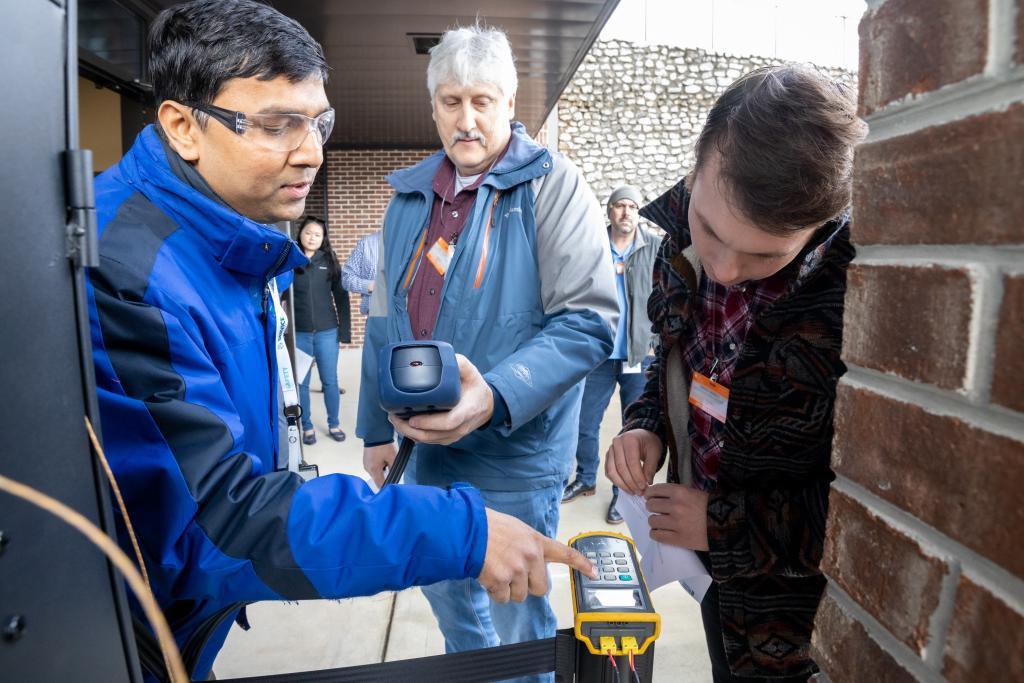
Road tested
Nimbalkar spent a few months in 2023 documenting how Better Plants program industry partners have put the Energy Bootcamp training into action. He visited industries that accepted DOE's Better Climate Challenge to set a GHG reduction goal of 50% within the next decade as part of the Road Show YouTube series. Nissan North America Inc.'s Chris Goddard, an energy and environmental engineering manager, showed Nimbalkar how a 6 million-square foot manufacturing plant with 7,000 employees in Smyrna produces 640,000 vehicles annually while reducing GHGs and energy intensity by 15%.
"We converted to a combination of battery-operated and electric tools to get off of compressed air," Goddard added. "And we've implemented a program called the Compressed Air Brigade focused on compressed air only, and they have maintenance folks with them to detect the leaks and do the repair on the spot, if possible."
Nissan has also addressed boilers, moving away from coal-fired boilers and operating on natural gas, which is much more efficient and emits less carbon. The plant is also looking into electrification options. In addition, Nissan has improved the painting process, integrating what they've termed "three wet processes" for applying automobile paint that has equated to 30% less energy consumption.
Nissan is also an example of how both GHG and energy intensity goals can be met by improving several manufacturing processes simultaneously.
"Just by limiting the number of steps in the painting process, Nissan also impacted natural gas consumption, air handling and electricity load," Nimbalkar said. "That translates to big savings in a relatively short amount of time."
Training impact
As reducing industrial carbon emissions continues to play a primary role in improving the overall energy efficiency of manufacturing industries, decarbonization training will become essential to success. That's something recent Decarbonization Bootcamp participant Tamara Cook sees as the starting point. Cook is the senior sustainability manager for Leggett & Platt, a Missouri-based manufacturer of home and automobile components.

"The training was very timely in that it provided relevant information and approaches for industrial decarbonization and carbon management," Cook said. "I also learned how to develop a GHG emissions reduction plan and the key decarbonization pathways available to consider to meet our goals. These were all very valuable takeaways, as our team is currently working to develop an emissions reduction plan."
For Rishabh Bahel, the energy and environmental manager with Nestlé, Better Plants program training has been essential to helping his company reach its carbon emissions reduction goals in the U.S.
"As part of the Better Climate Challenge program, Nestlé Health Science and Nestlé USA have achieved more than a 25% reduction in emissions from our 2018 base year," Bahel said. "To achieve this, our teams have implemented several projects across our factories, ranging from lighting efficiency to boiler combustion tuning to help ensure reduction stays an integral part of our energy strategy."
Energy-monitoring software tools, such as the Energy Footprint Tool introduced during Energy Bootcamps, can be shared throughout companies like Nestlé, too.
"We meet industry wherever they are in their energy efficiency journey. At the very beginning or far down the road, it doesn't matter," Nimbalkar said. "Our goal is to help remove obstacles and make it easier to achieve the end result, which is a more sustainable company that's saving energy, lowering costs and improving the environment."
UT-Battelle manages ORNL for DOE's Office of Science, the single largest supporter of basic research in the physical sciences in the United States. The Office of Science is working to address some of the most pressing challenges of our time. For more information, please visit energy.gov/science.