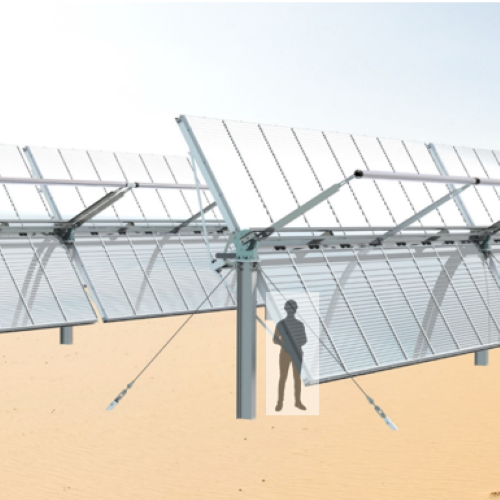
Industry and academia are collaborating to build a world-first, cost-effective concentrated solar thermal (CST) demonstrator that is set to transform Australia's industrial heat sector by reducing its reliance on fossil fuels.
Using lightweight plastic mirrors to focus sunlight on a specific target to create the necessary heat needed for industrial processes, the University of South Australia (UniSA) has joined forces with Impacts Renewable Energy Pty Ltd and Charles Sturt University (CSU) on the clean energy project.
Leveraging more than a decade of research into durable, weather-resistant reflective coatings, the project - funded by the Federal Government's Australia's Economic Accelerator (AEA) Ignite program - will fabricate and install a novel, two-module CST demonstrator incorporating the mirrors.
These mirrors, created through patented UniSA technology, offer an affordable and easily transportable alternative to traditional glass-based solar thermal systems. They generate heat that can either be applied directly in industrial processes or to heat water to create steam to power a turbine and produce electricity.
"Industrial process heat accounts for a staggering 25% of global energy use and 20% of CO2 emissions," says project lead Dr Marta Llusca Jane.
"Unfortunately, most renewable energy technologies - like photovoltaics - fall short of meeting the high-temperature demands of these sectors. Our plastic-based CST technology fills that gap and does so with significant cost and installation advantages."
The project's first phase will see two full-scale models - each made up of 16 thermoformed and coated panels - constructed, installed and tested at CSU's "Vineyard of the Future".
The panels incorporate a multilayer aluminium-silica reflective coating developed by UniSA's Future Industries Institute, applied via a physical vapour deposition to ensure durability and optimal solar reflectivity.
Unlike conventional solar thermal systems that require heavy infrastructure to support fragile glass mirrors, this new system features Impacts' durable, patented lightweight plastic mirror panels that can be flat-packed, transported, and assembled with ease.
The goal is to generate solar thermal energy at temperatures between 100°C and 400°C - ideal for processes such as food production, grain and pulse drying, sterilising, solar desalination, mining sites, polluted groundwater remediation and wastewater treatment.
Dr Llusca Jane says the AEA funding is critical to the project's success.
"Without this funding, the technical and financial risks of early-stage commercialisation would be too high for private investors. This demonstrator will allow us to scale the technology for real-world applications," she says.
The second stage, to be pursued under the AEA's Innovate program, will see a larger, commercial-scale pilot tested with key agribusiness and industrial partners. Strong interest has already been expressed by several national and international producers, highlighting the technology's outstanding commercial potential.
Industry Professor Colin Hall, inventor of the plastic mirror coating technology currently used in the automotive industry, says the time is ripe for such innovation.
"We're seeing record fossil fuel prices and increasing pressure for industries to decarbonise," Prof Hall says. "This CST solution is uniquely suited to Australia's hot, dry climate and offers a viable pathway to zero-emissions process heat."
With the potential to reduce the cost of renewable process heat for agribusiness and industry by 40% and unlock export opportunities for Australian manufacturing, Dr Llusca Jane says the project signals a green industrial future.
"By proving this technology in the field, we are laying the foundation for a cleaner, more resilient energy system across Australia and beyond."