Late last year, Caltech researchers revealed that they had developed a new fabrication technique for printing microsized metal parts containing features about as thick as three or four sheets of paper.
Now, the team has reinvented the technique to allow for printing objects a thousand times smaller: 150 nanometers, which is comparable to the size of a flu virus. In doing so, the team also discovered that the atomic arrangements within these objects are disordered, which would, at large scale, make these materials unusable because they would be considered weak and "low quality." In the case of nanosized metal objects, however, this atomic-level mess has the opposite effect: these parts can be three-to-five-times stronger than similarly sized structures with more orderly atomic arrangements.
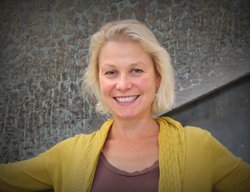
Julia Greer Credit: Caltech
The work was conducted in the lab of Julia R. Greer, the Ruben F. and Donna Mettler Professor of Materials Science, Mechanics and Medical Engineering; and Fletcher Jones Foundation Director of the Kavli Nanoscience Institute. It is described in a paper appearing in the journal Nano Letters.
The new technique is similar to another announced by the team last year, but with each step of the process reimagined to work at the nanoscale. However, this presents an additional challenge: the manufactured objects are not visible to the naked eye or easily manipulatable.
The process starts with preparing a photosensitive "cocktail" that is largely comprised of a hydrogel, a kind of polymer that can absorb many times its own weight in water. This cocktail is then selectively hardened with a laser to build a 3-D scaffold in the same shape as the desired metal objects. In this research, those objects were a series of tiny pillars and nanolattices.
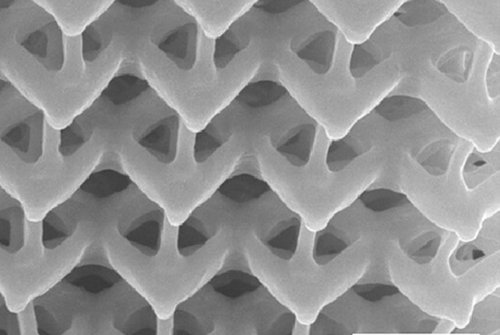
A nanoscale lattice prepared using a new technique developed by the lab of Julia R. Greer. Credit: Caltech
The hydrogel parts are then infused with an aqueous solution containing nickel ions. Once the parts are saturated with metal ions, they are baked until all the hydrogel is burned out, leaving parts in the same shape as the original, though shrunken, and consisting entirely of metal ions that are now oxidized (bound to oxygen atoms). In the final step, the oxygen atoms are chemically stripped out of the parts, converting the metal oxide back into a metallic form.
In the last step, the parts develop their unexpected strength.
"There are all these thermal and kinetic processes occurring simultaneously during this process, and they lead to a very, very messy microstructure," she says. "You see defects like pores and irregularities in the atomic structure, which are typically considered to be strength-deteriorating defects. If you were to build something out of steel, say, an engine block, you would not want to see this type of microstructure because it would significantly weaken the material."
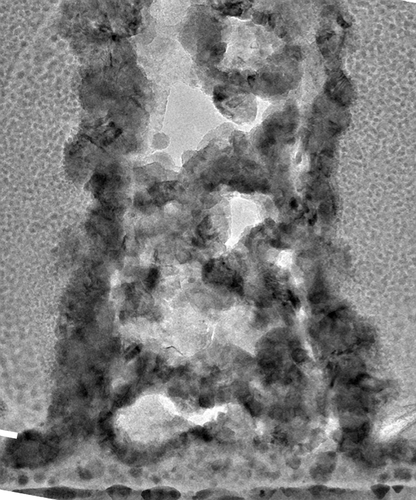
The irregular interior structure of a nanoscale nickel pillar. Credit: Caltech
However, Greer says they found exactly the opposite. The many defects that would weaken a metal part at a larger scale strengthen the nanoscale parts instead.
When a pillar is defect free, failure occurs catastrophically along what is known as a grain boundary-the place where the microscopic crystals that make up material butt up against each other.
But when the material is full of defects, a failure cannot easily propagate from one grain boundary to the next. That means the material won't suddenly fail because the deformation becomes distributed more evenly throughout the material.
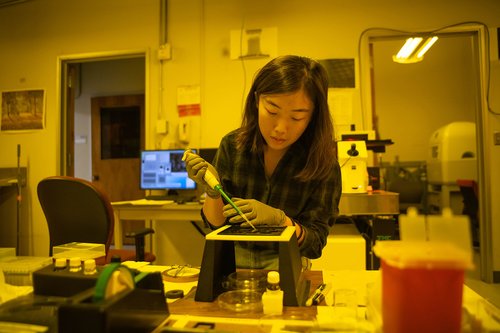
Mechanical engineering graduate student Wenxin Zhang works in the nano-fabrication lab. Credit: Caltech
"Usually, the deformation carrier in metal nanopillars-that is, a dislocation or slip-propagates until it can escape at the outer surface," says Wenxin Zhang, lead author of the work and a graduate student in mechanical engineering. "But in the presence of interior pores, the propagation will quickly terminate at the surface of a pore instead of continuing all the way through the entire pillar. As a rule of thumb, it's harder to nucleate a deformation carrier than to let it propagate, explaining why the present pillars may be stronger than their counterparts."
Greer believes that this is one of the first demonstrations of 3-D printing of metal structures at the nanoscale. She notes that the process could be used for creating many useful components, such as catalysts for hydrogen; storage electrodes for carbon-free ammonia and other chemicals; and essential parts of devices such as sensors, microrobots, and heat exchangers.
"We were originally worried," she says. "We thought , 'Oh my, this microstructure is never going to lead to anything good,' but apparently, we did not have a reason to worry because it turns out it's not even a detriment. It's actually a feature."
The paper describing the work, "Suppressed Size Effect in Nanopillars with Hierarchical Microstructures Enabled by Nanoscale Additive Manufacturing," appears in the August issue of Nano Letters. Coauthors are Wenxin Zhang (MS '22); Thomas T. Tran (MS '22), materials science graduate student; Rebecca A. Gallivan (MS '22, PhD '23), formerly of Caltech and now with ETH Zürich; Zhi Li of the Institute of High Performance Computing in Singapore; and Ruoqi Dang and Huajian Gao of Nanyang Technological University and the Institute of High Performance Computing in Singapore.
Funding for the research was provided by the U.S. Department of Energy.