Porous materials have a wide range of applications due to their capacity to act as filters, or lightweight structural materials that use less material than a solid substance. Researchers including those from the University of Tokyo created a new material fine enough to filter things like viruses but is strong enough to be a rigid construction material for devices. What makes this material unique is, it can be flexible when wet and responds to changes in pH. This and the fact it can be coated onto other substances give rise to a new range of functional and safe materials which use the minimal amount of raw material to create, leading to more sustainable manufacturing possibilities.
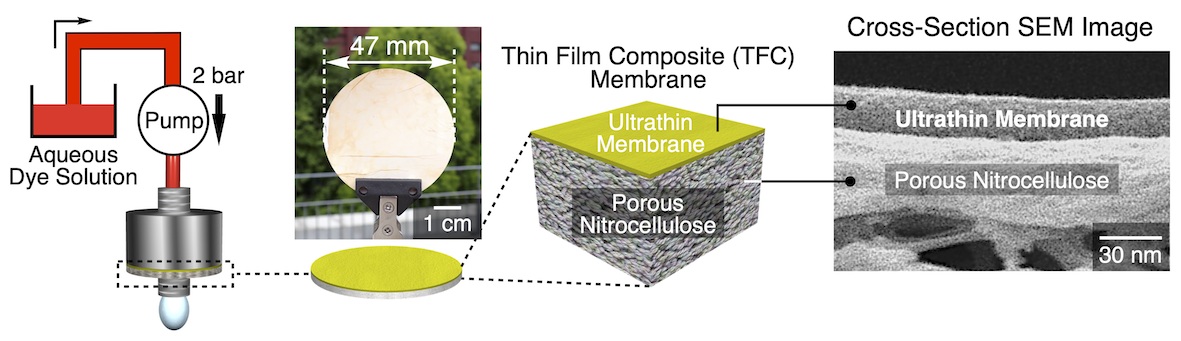
You've probably seen a loofah sponge at some point, those coarse, tough, weblike things hanging in peoples' bathrooms. Given their rigid, fibrous nature, you would be forgiven for thinking they are made of some kind of plastic or synthetic material. But believe it or not, the humble loofah sponge is actually the dried-out skeleton of a kind of melon often called an Egyptian cucumber. What makes their desiccated husks so useful, though, is that they are strong when dry, flexible when wet, and dry quickly, which helps resist mold buildup. Some of these properties can be useful in materials made for very different purposes, such as in the manufacture of devices.
"We developed a lightweight yet mechanically robust porous polymer, which resembles the fiber network of a natural loofah sponge. Though we did not set out to create something with such an appearance, it was a pleasant surprise," said Associate Professor Yoshimitsu Itoh from the Department of Chemistry and Biotechnology at the University of Tokyo. "So-called polymer materials like this already exist in nature, but we wanted to create something synthetic as it affords us control over its properties such that we can give it various useful functions."
Itoh and his team created a polymer network which can be useful as a filter as the network is dense enough to allow fluids to pass but block objects, including bacteria and viruses (which are also killed). This is desirable as currently, filters for this are often made out of less-sustainable materials, but this synthetic loofah is made from a substance similar to lignin, which is a basic component of wood. Although the team has not yet investigated the safety of the material, it is safe for human contact.
"One drawback of lightweight polymers is their mechanical weakness — they tend to be very soft," said Itoh. "But ours is low density, only half a gram of material per cubic centimeter, but has a stiffness of 11 gigapascals — for reference this is perhaps four times stronger than that of an ordinary polymer. This means it could be used to create devices where strength is really key, without having to resort to denser, heavier and less-sustainable materials."
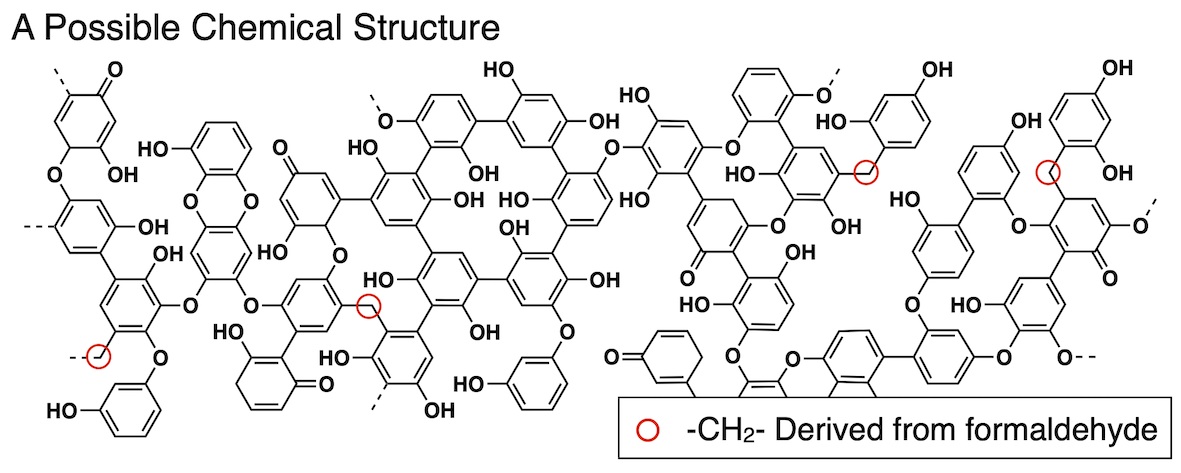
But there's scope for even greater functionality, as the team is also creating a thin porous carbon membrane by baking the membrane in an inert atmosphere. This could give engineers a material to make nanoscale, functional electronic components, such as microcapacitors, more efficiently and with greater structural characteristics. Another possibility is for the polymer to have some dynamic properties, things that change with time due to the presence of something else. In this case, certain changes in pH, acidity or alkalinity, can make the polymer more or less rigid, essentially allowing a portion of material to become more or less porous.
"In principle, this material we created could find many uses, though we have many steps to take before contemplating industrial integration of any kind," said Itoh. "But the production is very cheap and easy to perform, using only pure water with a voltage applied, and a mixture of deprotonated resorcinol and an aldehyde, which spontaneously combine to make an ultrathin membrane with a loofah-like appearance under an electron microscope. One big advantage of this membrane is that there is no need for post-processing. Usually, thin films are made by first synthesizing the bulk polymer and then processing it into a film. Our method can directly give the product the form of a thin film and is, in principle, applicable to roll-to-roll processing. This is a big advantage for the production."