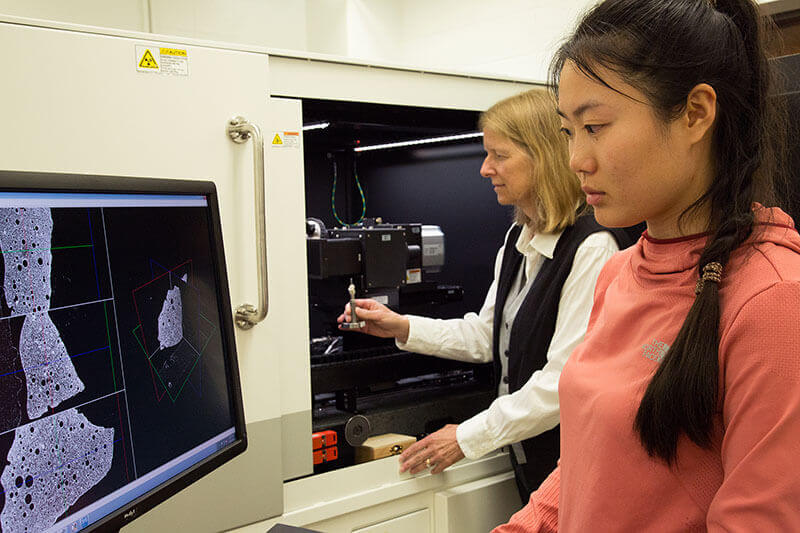
Purdue University professor Laura Pyrak-Nolte and physics graduate student Liyang Jiang use a 3D X-ray microscope to examine and analyze created mineral samples. (Purdue University photo)
Note to Journalists: A photo of professor Laura Pyrak-Nolte and graduate student Liyang Jiang analyzing mineral samples is available in a Google Drive folder at https://purdue.university/2RkPmFE. For a copy of the research paper, contact Steve Tally at [email protected].
WEST LAFAYETTE, Ind. — Cracks are everywhere, and they often mean trouble. In the foundation of your house, in your windshield, in the tectonic plates below your feet. But, surprisingly, scientists don't actually understand them as well as they would like.
Purdue physics professor Laura Pyrak-Nolte and her lab team works with Purdue's Rock Physics Research Group to better understand how and where fractures form. Being able to predict and understand fractures is vitally important to a wide range of fields, including improving the safety and efficacy of natural gas production, carbon sequestration, and nuclear waste disposal. It's also important in improving the structural integrity of large 3D-printed components, including bridges and human habitats on other planets.
In nature, rocks contain a wide variety of features and a diverse array of unique qualities. Among them are the way the layers of minerals form, as well as the orientation of the "mineral fabric"— the way the mineral components that make up rock layers and formations are organized.
Pyrak-Nolte and physics graduate student Liyang Jiang study fracture formation patterns by using 3D printers, with other team members that include Antonio Bobet, Purdue's Edgar B. and Hedwig M. Olson Professor in Civil Engineering, and Hongkyu Yoon, a technical expert at Sandia National Laboratories.
"Given that fracture geometry is so important, a key question is what affects this geometry as a fracture forms in rock?" Pyrak-Nolte asks. "Our work centers on the question of whether we can detect fractures remotely and whether we can predict how they form, and can we learn about their fracture geometry from their mineral composition? Our colleagues had a way to print synthetic rocks out of gypsum, so we could 3D-print rocks with repeatable features."
Many people are familiar with the idea of using a 3D printer to create plastic items, but fewer realize that you can use a 3D printer to create synthetic rock samples. Such 3D-printed rock samples help physicists and engineers study rocks, as they help keep the variables of the experiment controlled.
All 3D-printed substances are made up of layers. In this case, the printer puts down a layer of bassanite powder — a calcium sulfate mineral — and, just like an inkjet printer, it goes across spraying a binder, then putting another layer of bassanite on top of it. This printing process induces chemical reaction of bassanite powders with water-based binder solution. The result is a gypsum sample that has layers bound together by gypsum crystals. The power of the process is that researchers can use a computer program to control the quality of every aspect of the synthetic rock.
Before 3D printing technology, scientists either had to study rock samples from nature or casts formed by mixing mineral powder and water. Neither set of samples could be relied upon to be uniform, nor to deliver quantifiable, repeatable results needed to draw firm conclusions about rock mechanics.
"Our team was testing some rocks from natural rock formations," Jiang said. "But even if you get two samples very close to each other in location, they will be a bit different. They have all kinds of minerals with natural differences. You may have pre-existing fractures that you don't know about. Because of the new 3D printing technology, we're able to test rocks and gather reproducible results. We can design the shape in all dimensions. And it's a much more accurate process than working with natural rock or casts of rock."
The team was printing samples with various orientations of mineral fabric, determining if the orientation had any effect on how and where fractures formed when the sample was subjected to tension. Then Jiang noticed an intriguing pattern.
"Just by looking at the way the sample broke — the kind of fracture, its shape and smoothness — I could tell which 3D-printed rock sample I was looking at," Jiang said.
When a rock fractures, it tries to resist that breaking force. Jiang discovered that when the layers and minerals of the rock are oriented in the same direction and a certain kind of stress is applied, corrugated fractures tend to form. Corrugation is what it sounds like — a sort of sine-wave shape like the inner layers of a corrugated cardboard sheet. These corrugations form in nature, especially in sedimentary rocks.
After observing the phenomenon, the team tested randomly generated rock samples made with a traditional casting method. They discovered that in rock samples with no layers and no oriented grains, fractures formed smoothly, with no corrugations. However, different roughnesses emerged in each sample because of the different mechanical qualities in the rock.
"The key idea is that if we understand how corrugations are produced, just by looking at a rock sample we can remotely predict fracture geometry and preferential flow paths for fluids," Pyrak-Nolte said.
It works the other way, too. By looking at the way a rock fractures, researchers can infer something about its mineral orientation.
The team published these results in Scientific Reports.
Jiang, Pyrak-Nolte and their team will continue to use 3D-printed rock samples to study fracture geometry and the way rocks break. This ongoing research was supported by the Laboratory Directed Research and Development program at Sandia National Laboratories and U.S. Department of Energy, Office of Science, Office of Basic Energy Sciences, Geosciences Research Program.